Project Description: To build and assemble a TPI and DAF System for Lube Oil Blending Plant in Phillipine
Product Used in this Project:
Watterson Technology Sdn Bhd
Specialized in Water & Wastewater Treatment System



Okada Technology Sdn Bhd
Specialized in Sludge Dryer System
Okada Dryer Technical Specification
Refrigerant Heat Pump Hot Air Technology
OKADA Dryer Schematics
.png)
The OKADA Dryer operates through dehydration principle by circulating dry hot air at 50°C to 60°C through a designated volume of wet sludge cake. Water moisture from the wet sludge cake is adsorbed into the dry air is then pass through the dehumidifying unit where water moisture in the air is then condensed via an evaporator coil. The dry air is then reheat with a condenser coil which now have enormous water adsorbing capacity; it is then reintroduced into the drying chamber. The air is circulated in a closed-loop through the entire system without the need for an air emission control system. The refrigeration cycle of the combined energy of both cold and hot heat exchangers; gives an advantage of high energy efficiency in the drying process. Energy consumption is approximately 0.26 to 0.36 kWh for every kilogram of sludge dried.

The OKADA Sludge Bin is design to channel the hot air from the Hot Air Generator (HAG) into the sludge through the pockets of air created on the Stainless Steel slots. The Hot Air will then carry the warm moist air from the sludge into the cooling coil where the air is cooled and the moisture is removed. The air is then circulated back in the Heating Coil before being re-circulated into the sludge once more. It comes with 2 dumping systems which reduce manpower and risk of injuries
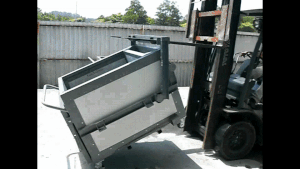
J-Hook Dumping System
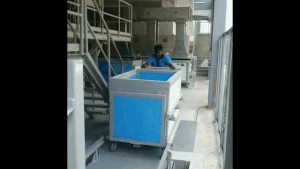
Tote Dumping System
The OKADA Dryer also comes with an auto-wash system. This system is designed to clean the cooling coil from dust and dirt which accumulates in the coil during operation. With the auto-wash system, it reduce the need for maintenance on the cooling coil and increases it's efficiency.
With increase efficiency of the cooling coil, the load on the compressor will be reduced, thus reducing the energy consumption. By having these features in the OKADA Dryer, it is guarantee to reduce the operational cost and prevent the corrosion of the cooling coil.
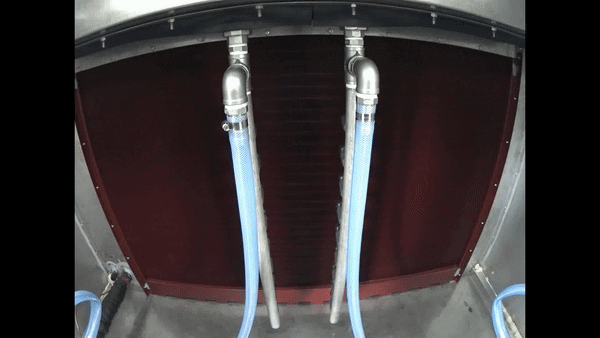
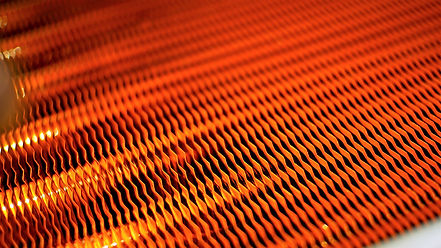
The OKADA Dryer Coils are coated with anti-corrosion coating. This coating is to protect the coils from acid moisture from the sludge thus increasing it's lifespan and longevity of the coil. It also to protect the coil from leakage due to corrosion caused by moisture build up.
We implement a full coating process where the anti-corrosion coating is poured on to the coil to ensure that it is fully coated inside and out.

Dryer Coil After Coating

Coating Process
OKADA Continuous Belt dryer is the latest invention where sludge is continuously dried and is discharge into a jumbo bag without the need of manpower. The reduction in moisture content in the sludge is made achievable by the use of shredder where sludge is shredded into peanut size shape to increase its surface area which in return accelerates the drying capability.
Sludge is transferred by means of belt conveyor system and air is blown through the conveyor belt to have an all round surface dryness.

Belt Conveyor
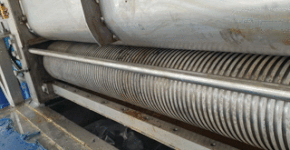
Sludge Shredder
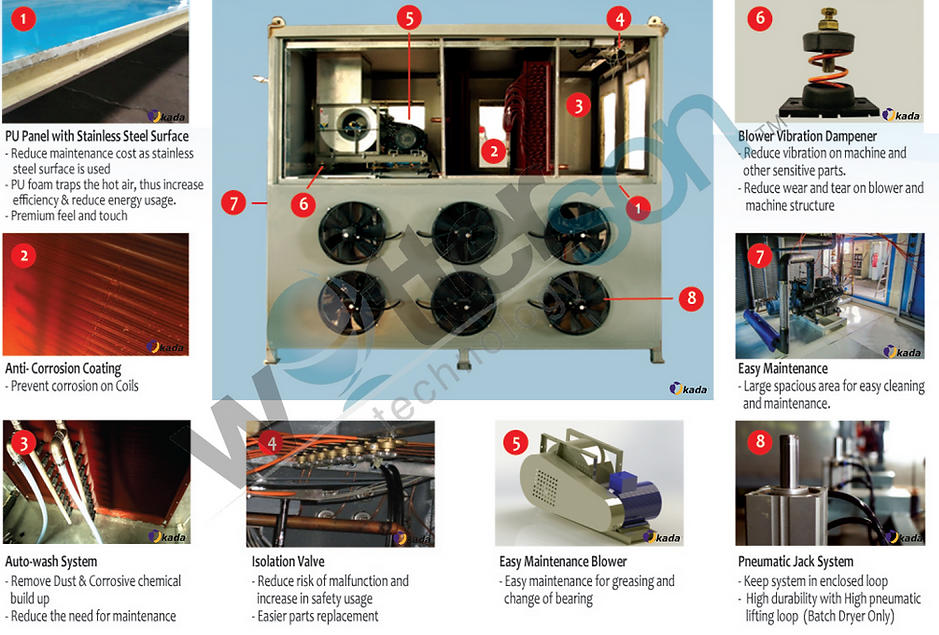